Demir çelik dökümü, endüstriyel üretimde önemli bir role sahip olan bir süreçtir. Bu süreçte, yüksek kaliteli ve güvenilir ürünlerin elde edilmesi için kalite kontrol yöntemleri büyük önem taşır. Demir çelik dökümünde kullanılan kalite kontrol yöntemleri, hataların erken tespit edilmesini ve üretim sürecinin verimliliğinin artmasını sağlar.
Kalite kontrolün ilk aşaması, ham malzemelerin analizidir. Demir cevheri ve diğer alaşımların bileşimi, özellikle karbon içeriği titizlikle incelenir. Doğru bileşim, istenen mekanik özelliklerin elde edilmesi açısından kritiktir.
Bir sonraki adım, erimiş demir çeliğin döküm işlemidir. Döküm sırasında, dökümhanede yer alan uzmanlar, özel ekipmanlar ve izleme sistemleri kullanarak döküm parametrelerini sürekli olarak kontrol ederler. Sıcaklık, basınç ve akış hızı gibi faktörler, kaliteli bir döküm için hassas bir şekilde ayarlanmalıdır.
Döküm tamamlandıktan sonra, üretilen parçaların geometrisel ve fiziksel özellikleri kontrol edilir. Boyut toleransları, yüzey pürüzlülüğü ve diğer özelliklerin belirlenmesinde ölçüm cihazları ve deneyler kullanılır. Bu aşamada, her bir parça görsel olarak incelenir ve kalite standartlarına uygunluğu değerlendirilir.
Son olarak, mekanik testler yapılır. Bu testler, demir çelik dökümünün dayanıklılığını, sertliğini ve mukavemetini değerlendirmek için gerçekleştirilir. Çekme testleri, eğilme testleri ve darbe testleri gibi yöntemler, ürünlerin performansının belirlenmesinde kullanılır.
Demir çelik dökümünde kalite kontrolü, sürekli bir süreçtir. Üreticiler, ISO standartları gibi uluslararası kabul görmüş kalite sistemlerine uygunluk sağlamak için düzenli olarak denetlenir. Ayrıca, geribildirimler ve iyileştirme çalışmalarıyla sürekli olarak kaliteyi artırmaya yönelik çabalar da devam eder.
Sonuç olarak, demir çelik dökümünde kalite kontrolü, güvenilir ve yüksek kaliteli ürünlerin elde edilmesi için kritik bir adımdır. Ham malzeme analizinden başlayarak döküm işlemi, ölçüm ve testlerle desteklenir. Bu süreçteki titizlik, hataların önlenmesini ve optimize edilmiş üretim verimliliğini garanti eder. Demir çelik dökümü endüstrisinde kalite kontrol yöntemlerinin etkin bir şekilde uygulanması, sektörün büyümesine ve gelişmesine katkıda bulunur.
Non-destrüktif testlerin demir çelik dökümündeki rolü
Non-destrüktif testler (NDT), demir çelik döküm sektöründe kritik bir rol oynamaktadır. Bu testler, yapısal bütünlük ve kalite kontrolünü sağlamak için kullanılan önemli araçlardır. Demir çelik dökümlerinin güvenliğini ve dayanıklılığını sağlamak amacıyla NDT yöntemleri sıklıkla uygulanmaktadır.
NDT’nin demir çelik dökümünde rolü çok yönlüdür. İlk olarak, bu testler kaynak hatalarını, çatlakları, gözenekleri ve diğer kusurları tespit etmek için kullanılır. Ultrasonik testler, manyetik parçacık testleri, radyografi gibi farklı NDT teknikleri, demir çelik dökümlerde oluşabilecek herhangi bir içsel kusuru tespit etme yeteneğine sahiptir. Bu sayede potansiyel sorunlar önceden belirlenerek, kalitesiz ürünlerin kullanılması veya olası felaketlerin önüne geçilebilir.
Bunun yanı sıra, NDT yöntemleri ayrıca malzeme karakterizasyonunda da kullanılır. Döküm yapıların mekanik özellikleri, yüzey sertliği, yoğunluk gibi faktörlerin değerlendirilmesi NDT ile mümkündür. Bu bilgiler, mühendislik tasarımlarında ve malzeme seçiminde önemli bir rol oynar. Demir çelik dökümünün belirli bir uygulama için uygunluğunu değerlendirmek ve kalite standartlarına uygunluğunu doğrulamak için NDT kullanılır.
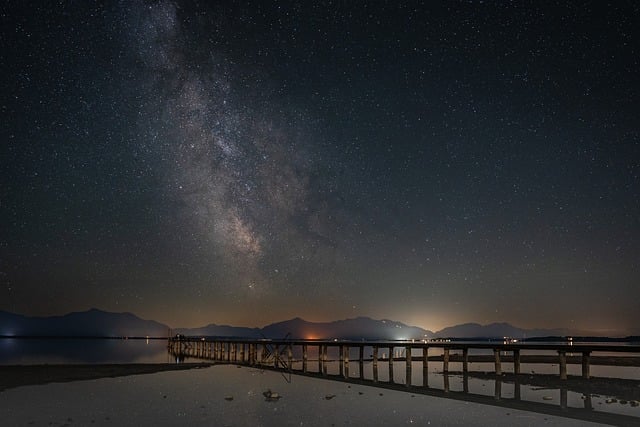
NDT’nin demir çelik dökümündeki önemi sadece kalite kontrolle sınırlı değildir. Aynı zamanda operasyonel verimliliği artırmak, enerji maliyetlerini düşürmek ve üretim süreçlerini optimize etmek için de bu testlerden faydalanılır. Örneğin, manyetik parçacık testleri ile döküm işlemi sonrasında oluşan çatlaklar hızlı bir şekilde tespit edilerek, zaman ve maliyet kaybına neden olan yeniden işleme ihtiyacını azaltır.
Sonuç olarak, non-destrüktif testler demir çelik döküm sektöründe hayati bir rol oynamaktadır. Bu testler sayesinde yapısal bütünlük sağlanır, malzeme karakterizasyonu yapılır ve kalite kontrolü sağlanır. NDT yöntemleri, demir çelik dökümünün güvenliğini, dayanıklılığını ve işletme verimliliğini artıran önemli araçlardır. Sektördeki gelişmelerle birlikte NDT teknikleri de sürekli olarak ilerlemekte ve daha etkili sonuçlar sunmaktadır.
Metallerin kimyasal analizleri ve kalite değerlendirmesi
Metaller, endüstriyel ve ticari birçok alanda önemli bir rol oynar. Bu nedenle, metallerin kimyasal analizleri ve kalite değerlendirmesi, malzemelerin uygunluğunu ve performansını belirlemek için kritik bir süreçtir. Bu makalede, metallerin kimyasal analizleri ve kalite değerlendirmesinin önemi ve süreci hakkında ayrıntılı bilgi sunulmaktadır.
Kimyasal analizler, metallerin bileşimini belirlemek için kullanılan yöntemlerdir. Bir metal örneği alındığında, laboratuvar ortamında çeşitli analiz teknikleri uygulanarak elementel bileşimi tespit edilir. Bunlar arasında spektroskopi, kütle spektrometrisi, atomik emisyon spektrometrisi ve X-ışını floresans spektrometrisi gibi yöntemler bulunur. Kimyasal analizler, metallerin işlenebilirlik, dayanıklılık, korozyon direnci ve diğer mekanik özellikleri üzerinde büyük bir etkiye sahip olan iz elementlerin varlığını ve miktarını da belirleyebilir.
Kalite değerlendirmesi ise bir metal ürününün belirli standartlara uygunluğunu kontrol etmek amacıyla gerçekleştirilen bir dizi test ve incelemedir. Bu değerlendirme süreci, metalin özellikleri ve performansı hakkında bilgi sağlar ve ürünün istenen kalite standartlarına uygunluğunu belirler. Kalite değerlendirmesi, çekme testleri, sertlik testleri, darbe dayanımı testleri ve mikroyapısal incelemeler gibi çeşitli teknikleri içerebilir.
Metallerin kimyasal analizleri ve kalite değerlendirmesi, endüstriyel uygulamalarda güvenilirlik, maliyet etkinliği ve üretim verimliliği açısından hayati öneme sahiptir. Bu süreçler, malzemelerin doğru seçimi, kalite kontrolü ve kalite iyileştirmesi için temel bilgileri sağlar. Ayrıca, metallerin kullanım ömrünü arttırarak güvenlik ve dayanıklılık açısından da büyük bir rol oynar.
Sonuç olarak, metallerin kimyasal analizleri ve kalite değerlendirmesi, metalürji endüstrisinde büyük bir öneme sahip olan kritik süreçlerdir. Bu analizler, metal bileşimi ve kalitesinin belirlenmesine yardımcı olurken, kalite değerlendirmesi ise ürünlerin uygunluğunu kontrol eder. Bu süreçler, endüstriyel uygulamalarda güvenilirlik, performans ve kalite standartlarının sağlanmasına katkıda bulunur.
Mekanik testlerin kalite kontrolünde kullanımı
Mekanik testler, kalite kontrol süreçlerinde önemli bir rol oynamaktadır. Bu testler, malzeme ve ürünlerin dayanıklılığını, performansını ve kalitesini değerlendirmek için kullanılan güvenilir bir yöntemdir. Mekanik testler, endüstriyel sektörlerde yaygın olarak kullanılmaktadır ve üretim sürecinin her aşamasında büyük bir öneme sahiptir.
Birincil amaçlarından biri, malzemelerin fiziksel ve mekanik özelliklerini belirlemektir. Bu testlerle, gerilme, sertlik, tokluk, elastisite, kırılma direnci gibi önemli parametreler ölçülerek, malzemelerin performansı hakkında bilgi sahibi olunur. Böylece, ürünlerin dayanıklılığı ve güvenilirliği açısından kritik bir rol oynayan bu özelliklerin belirlenmesi mümkün olur.
Mekanik testler, farklı endüstriyel sektörlerde geniş bir uygulama alanına sahiptir. Örneğin, otomotiv sektöründe araç parçalarının mukavemeti ve dayanıklılığı test edilirken, metalurji alanında malzemelerin mekanik özellikleri incelenir. İnşaat sektöründe ise yapı malzemelerinin performansı ve dayanıklılığı için mekanik testler büyük önem taşır.
Bu testlerin kullanımının kalite kontrol süreçleri üzerindeki etkisi büyük olabilir. Mekanik test sonuçlarına dayanarak, üretim aşamalarında hataların tespit edilmesi ve düzeltici önlemlerin alınması mümkün olur. Böylece, ürünlerin kalitesinin yükseltilmesi ve müşteri memnuniyetinin artırılması sağlanır.
Mekanik testler aynı zamanda standartların oluşturulmasında da önemli bir rol oynar. Uluslararası standartlar, malzemelerin ve ürünlerin belirli bir kalite seviyesini sağlaması için test yöntemlerini belirler. Bu standartlara uygunluğun sağlanması, ürün güvenilirliğini ve pazar kabulünü artırır.
Sonuç olarak, mekanik testlerin kalite kontrolünde kullanımı, üretim sektöründe önemli bir yer tutmaktadır. Bu testler sayesinde malzemelerin ve ürünlerin özellikleri değerlendirilerek, daha kaliteli ve güvenilir ürünlerin üretilmesi mümkün olur. Kalite kontrol süreçlerinde mekanik testlerin doğru ve güvenilir bir şekilde uygulanması, şirketlerin rekabet avantajını artırmasına yardımcı olur.
Yüzey muayenesi teknikleri ve önemi
Yüzey muayenesi, endüstrinin çeşitli alanlarında önemli bir adımdır. Ürünlerin, malzemelerin veya yapıların kalitesini ve güvenilirliğini sağlamak için kullanılan tekniklerin bir bütünüdür. Yüzey muayenesi, herhangi bir yüzeydeki hataları, kusurları, çatlakları veya diğer sorunları tespit ederek, olası arızaların ve maliyetli problemlerin önlenmesini sağlar.
Birçok farklı yüzey muayene tekniği mevcuttur ve her biri belirli bir amaç için en uygun olanını seçmek önemlidir. Görsel muayene, yüzey üzerindeki gözle görülür kusurları tespit etmek için kullanılan basit bir yöntemdir. Bu, insan gözünün doğal yeteneklerine dayanır ve genellikle ilk aşamada kullanılır.
Buna ek olarak, manyetik parçacık muayenesi ve sıvı penetrant muayenesi gibi non-destructive testing (NDT) yöntemleri de yaygın olarak kullanılır. Manyetik parçacık muayenesi, ferromanyetik malzemelerdeki yüzey kusurlarını tespit etmek için manyetik alanlar kullanırken, sıvı penetrant muayenesi ise yüzeydeki çatlakları veya poroziteyi belirlemek için penetrant maddelerin kullanılmasını sağlar.
Ultrasonik muayene, ses dalgalarını kullanarak yüzey altındaki kusurları tespit etmek için yaygın olarak kullanılan bir başka yöntemdir. Bu teknik, malzemenin iç yapısını inceleyerek çatlakları veya diğer sakıncaları tespit edebilir.
Yüzey muayenesi, birçok endüstride büyük bir öneme sahiptir. Havacılık, otomotiv, enerji, petrol ve gaz gibi sektörlerde kullanılan malzemelerin ve yapıların güvenliği için bu tekniklerin uygulanması zorunludur. Ayrıca, kalite kontrol süreçlerinin bir parçası olarak da yüzey muayenesi sıkça kullanılır.
Sonuç olarak, yüzey muayenesi teknikleri, ürünlerin ve yapıların güvenliğini sağlamak, kaliteyi artırmak ve maliyetli arızaların önüne geçmek için hayati öneme sahiptir. Görsel muayene, manyetik parçacık muayenesi, sıvı penetrant muayenesi ve ultrasonik muayene gibi farklı teknikler, yüzeylerdeki hataları tespit etmek ve düzeltici önlemler almak için kullanılır. Bu teknikler, endüstriyel süreçlerin etkinliğini artırmak ve sonuçta daha güvenilir ürünler ve yapılar üretmek için vazgeçilmezdir.
Boyut kontrolleri ve toleranslarının belirlenmesi
Boyut kontrolleri ve toleransları, üretim süreçlerinde büyük öneme sahip olan kritik unsurlardır. Bu kontroller, bir parçanın istenen boyutlara uygun olarak üretilip üretilmediğini belirlemek için kullanılır. Toleranslar ise parça ölçülerinde kabul edilebilir sapmalara izin veren değerlerdir. Bu makalede, boyut kontrollerinin ve toleransların belirlenmesinin önemi ve nasıl yapıldığına dair ayrıntılı bir şekilde ele alınacak.
Boyut kontrolleri, imalat sektöründe kalite kontrolü sağlamak için temel bir araçtır. Üretim sırasında her bir parçanın spesifikasyonlara uygun olması gerekmektedir. Boyut kontrolleri, parçaların doğru ölçülerde üretildiğini teyit etmek için kullanılan yöntemlerden biridir. Bu kontroller genellikle özel ölçüm aletleri ve cihazlar kullanılarak yapılır.
Toleranslar ise parçaların istenen boyutlarına tam olarak uymasını beklemek yerine kabul edilebilir sapmaları belirler. Herhangi bir üretim sürecinde mükemmel bir kesinlik elde etmek zordur, bu nedenle toleranslar, üretimde ortaya çıkabilecek hataları ve sapmaları dikkate alarak tasarlanır. Toleranslar, montaj işlemlerinde parçaların bir araya gelmesini kolaylaştırır, işlevselliklerini artırır ve maliyetleri düşürür.
Boyut kontrolleri ve toleransların belirlenmesi için çeşitli yöntemler mevcuttur. Bu yöntemler genellikle tasarım mühendisleri tarafından kullanılır ve imalat sürecinin gereksinimlerine bağlı olarak belirlenir. Ölçüm aletleri, kalibrasyon standartları ve özel yazılımlar gibi araçlar kullanılarak boyut kontrolü gerçekleştirilir. Toleranslar ise tasarım ve üretim standartlarına dayanarak belirlenir.
Boyut kontrolleri ve toleransların doğru bir şekilde belirlenmesi, üretim süreçlerinde güvenilirlik, kalite ve verimlilik sağlar. Yanlış veya eksik boyut kontrolleri, hatalı parçaların üretilmesine ve kalite sorunlarına yol açabilir. Ayrıca, toleransların uygun bir şekilde ayarlanmaması durumunda, montaj problemleri ve işlevsellik sorunları ortaya çıkabilir.
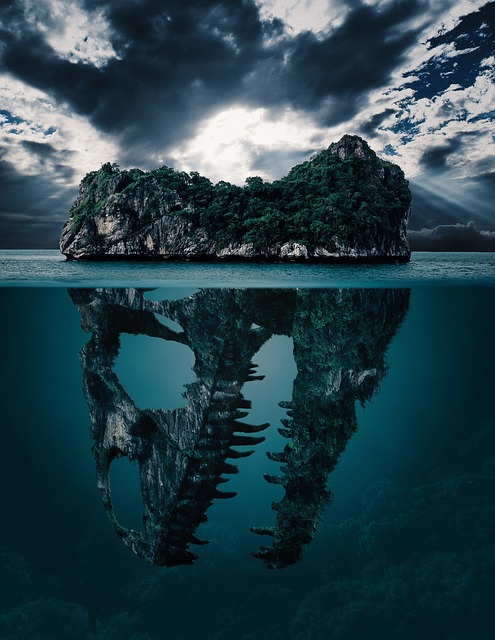
Sonuç olarak, boyut kontrolleri ve toleransları, üretim süreçlerinde vazgeçilmez unsurlardır. Doğru boyut kontrolü ve tolerans belirleme yöntemleri kullanılarak, kaliteli ve uyumlu parçaların üretimi sağlanabilir. Bu da üreticilerin müşteri memnuniyetini artırmasına ve rekabet avantajı elde etmesine yardımcı olur.
Kalibrasyon ve doğrulama prosedürleri
Kalibrasyon ve doğrulama prosedürleri, birçok endüstriyel alanda kritik öneme sahip olan güvenilirlik ve doğruluğu sağlamak için kullanılan yöntemlerdir. Bu prosedürler, ölçüm cihazlarının doğru sonuçlar vermesini sağlayarak üretim süreçlerinde ve kalite kontrolünde güvence sağlar.
Kalibrasyon, bir ölçüm cihazının doğruluğunu belirlemek ve ayarlamak için gerçek değerlerle karşılaştırılmasıdır. Bu işlem, ölçüm cihazının zaman içindeki sapmalarını tespit ederek düzeltme yapılmasını sağlar. Doğru kalibrasyon, ölçümlerin güvenirliğini artırır ve hatalı sonuçların önüne geçer.
Doğrulama ise kalibrasyon sonrasında yapılan bir süreçtir. Kalibre edilen cihazın performansının belirlenen spesifikasyonlara uygun olduğunu onaylar. Doğrulama süreci, ölçüm cihazının hassasiyetinin sınanması ve dayanıklılığının test edilmesini içerir. Böylece, cihazın kullanıma uygun olduğunu ve doğru sonuçlar vereceğini garanti altına alır.
Kalibrasyon ve doğrulama prosedürleri, birçok sektörde yaygın olarak kullanılmaktadır. Örneğin, tıbbi cihazlar, otomotiv endüstrisi, havacılık sektörü, gıda ve ilaç üretimi gibi alanlarda kalibrasyon ve doğrulama büyük önem taşır. Bu prosedürler, hasta güvenliğini sağlamak, üretim kalitesini iyileştirmek ve standartları karşılamak için kullanılır.
Kalibrasyon ve doğrulama süreçlerinin başarılı olması için uygun ekipman, yetkin personel ve belirlenen standartlara uygunluk şarttır. Ayrıca, bu prosedürlerin düzenli olarak tekrarlanması da önemlidir. Zamanla ölçüm cihazlarının performansı değişebilir, bu nedenle periyodik kalibrasyon ve doğrulama işlemleri yapılmalıdır.
Sonuç olarak, kalibrasyon ve doğrulama prosedürleri, ölçüm cihazlarının doğruluğunu ve güvenirliğini sağlayarak endüstriyel süreçlerde kritik bir rol oynamaktadır. Bu prosedürlerin doğru bir şekilde uygulanması, kalite kontrolünü artırır, hataları en aza indirir ve müşteri memnuniyetini sağlar. Kalibrasyon ve doğrulama, işletmelerin rekabetçiliklerini artırmalarına ve maliyetleri azaltmalarına yardımcı olur.